For efficient production of parts that require high-precision cutting, the steel specialist Ferro Service invested in two fiber laser systems that enable automatic weld edge preparation in a range of material thicknesses.The 2020 founded company Ferro Service Sp z o.o from Gubin (Poland) dedicates its services to mass production of laser cut parts – both straight and bevel. In order to improve its production efficiency, the steel specialists set out to look for state-of-the-art laser bevel cutting machines. After an intensive market research, they found the right solution: two fiber laser cutting machines from the MicroStep MSF Pro series with work areas of 3,000 x 1,500 mm. Both systems have been producing in multi-shift operation from the beginning.
Ferro Service manufacture parts for vehicles, crane arms or aerial work platforms that are used in various industries. The metalworking specialist based in Gubin supplies mass-produced components for its partner companies Ferro Umformtechnik GmbH & Co.KG, which operate in the steel processing sector, and the component manufacturer TEKRA Sp.z o.o.
3 production halls with a total area of 8,000 m²The recently established company planned the construction of 3 production halls with a total area of 8,000 m². The first hall with an area of 2,200 m², where the new MSF Pros are located, has been completed in March 2020. The other two halls – with one of them having an area of more than 2,600 m² – are currently under construction and their completion is scheduled for the end of June 2022. In addition to the investments in the new production site, the company also focuses on introduction of automation to its machinery park. The company had 44 employees initially – two years later it's already more than 75.
"Our strength is that we can offer full machining services," says CEO Matthias Bijkerk. After all, the company’s shareholder Ferro Umformtechnik is one of the technological leaders in the field of construction, sheet metal processing, components and assemblies.

Beveling in high demandMicroStep laser cutting technology is the heart of production in Ferro Service.
"Our main focus is the production of laser-cut beveled parts. We also offer plasma and oxyfuel cutting, bending and mechanical processing. 80 to 90 % of our production are parts for crane jibs," says Bijkerk. With a combination of different technologies and a wide range of machining, Ferro Service can produce many custom-made parts under one roof.
"We have created an important market position in production of small parts, which our customers appreciate," explains Matthias Bijkerk.
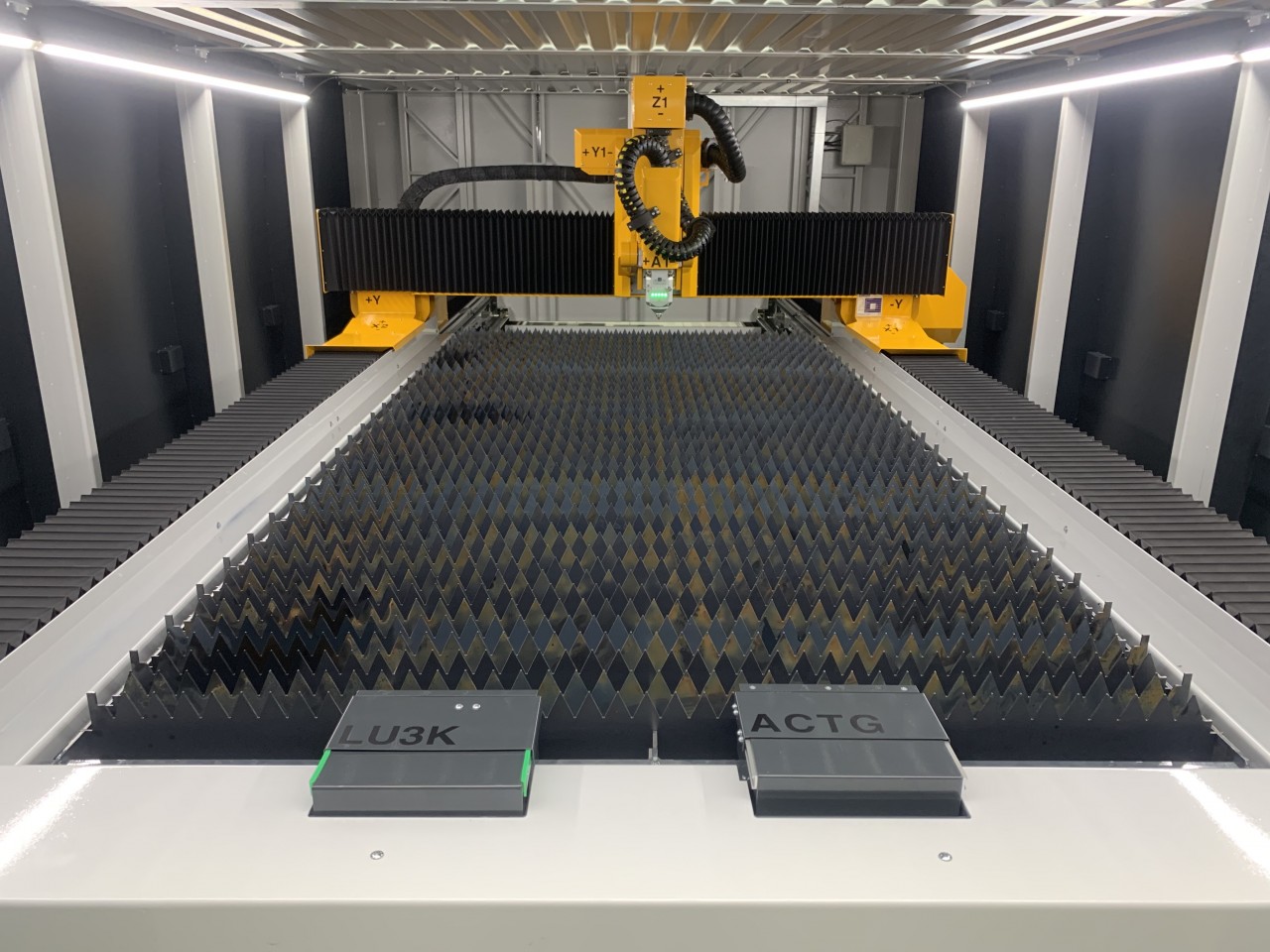
For laser cut parts, the company relies on two identical 3D laser cutting systems MSF Pro from MicroStep, with work areas of 3,000 x 1,500 mm.
"We were looking for an efficient, modern 3D laser cutting system to set up automated production," says Bijkerk. The decision-makers sought after a suitable solution through different channels and from different manufacturers until only two stayed in the race.
"When it comes to a machine with a laser cutting head that can cut bevels, there are not many manufacturers in the market that meet these conditions," added Bijkerk.
"We visited many manufacturers. However, the meetings and live demonstrations, among them a visit to the MicroStep headquarters in Bratislava, the quality of cut samples and a price analysis made us decide for the two laser cutting machines with bevel heads from MicroStep," acknowledges Bijkerk. In the future, the machines are prepared for adding an automated handling and material storage system, which will improve the automation of the production even further.
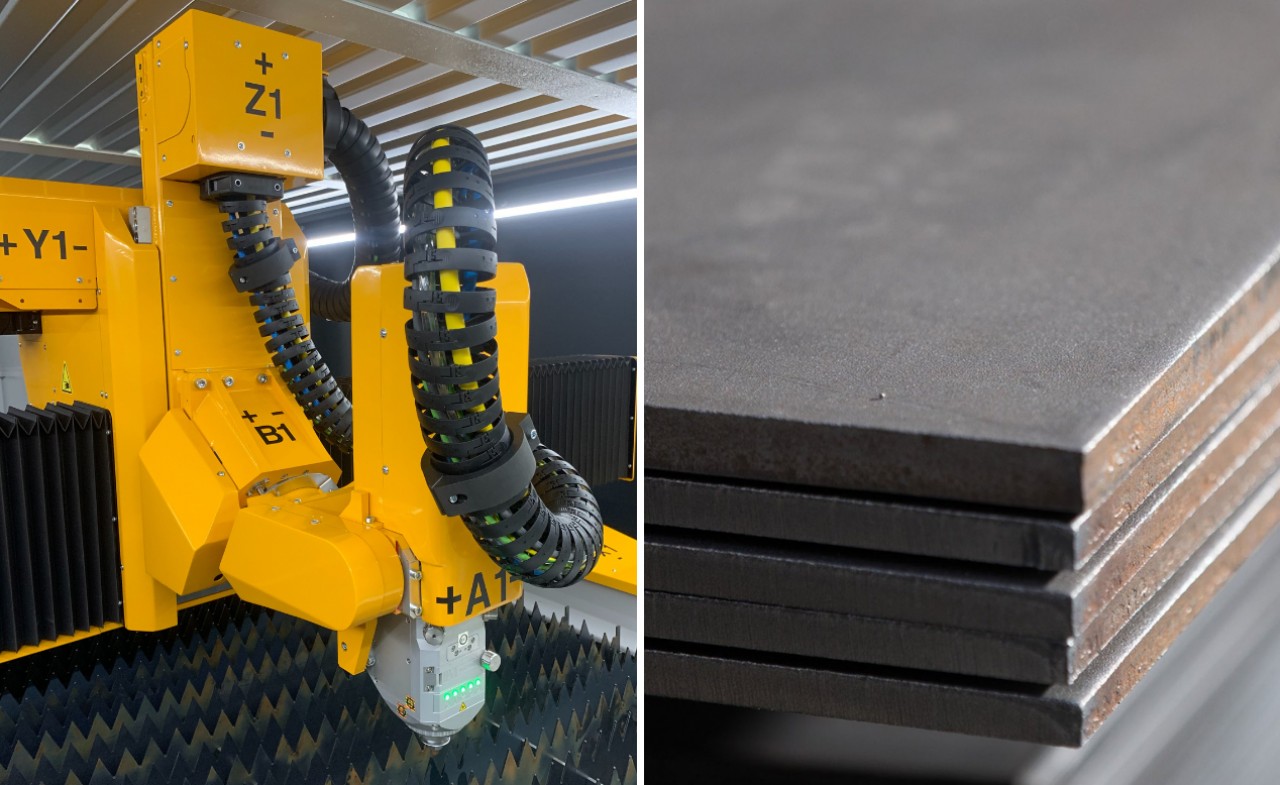
CNC cutting machines work in a three-shift operation, processing mainly orders for serial production of parts from fine-grained, high-strength and wear-resistant steels. The processed sheet metal thicknesses are mainly in the range from 1.5 mm to 15 mm. The machines also cut thicker materials, but Ferro Service has decided to use a plasma-oxyfuel cutting system for parts with thicknesses over 20 mm up to 100 mm.
The start was a success – two laser systems have been in production for almost two years.
"To sum it up, we are very, very satisfied. It all worked out nicely."