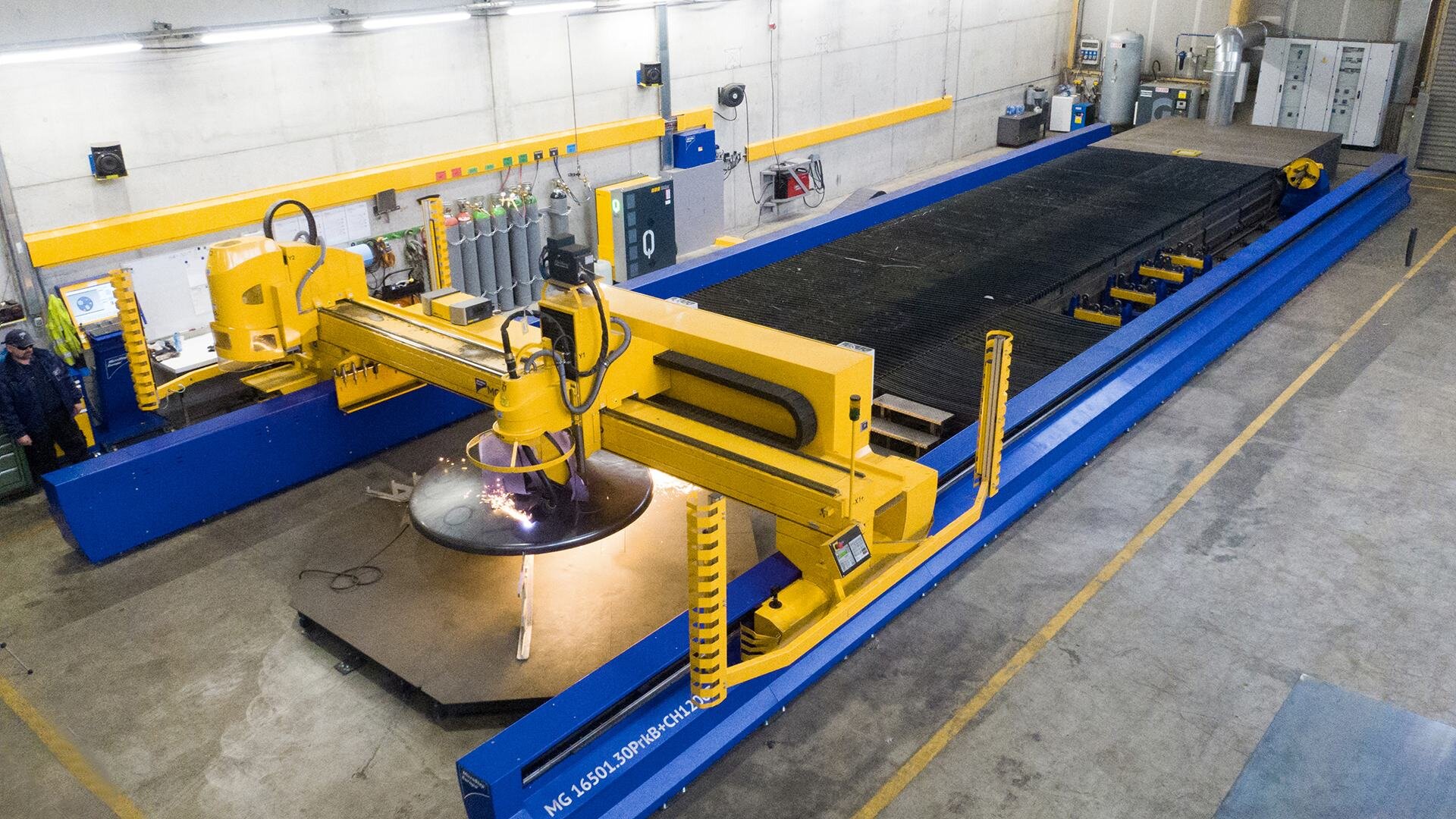
New machine MG 16501.30PrkB at Kammerer Tankbau is capable of processing sheet metal, pipes, closed profiles and domes.
Founded as a tinsmith business more than 75 years ago,
Kammerer Tankbau GmbH of South Tyrol has developed into a sought-after company in the field of tank and cistern production. Customers from various industries all over Europe trust their products: sheet metal tanks for fuel, stainless steel tanks for drinking water, bulletproof tanks, pellet or AD Blue tanks, just to name a few. Through the use of innovative technologies, the family business, now in its third generation, is constantly developing new products, expanding its broad portfolio. It is not uncommon to see giants 30 m long with a diameter of 4 m take shape in the Kammerer Tankbau´s over 12,000 m² factory. The signature green fiberglass coating, a unique selling point, makes the products particularly durable and robust. In addition to its standard product portfolio, the company designs and manufactures custom components according to specific requirements.
"When manufacturing a tank bottom, we save a day of time compared to the previous manual cutting."
Plate, pipe and dome processing on one machineFor decades, the sheet metal required for the containers was cut by hand or outsourced to steel service centers. "Constantly full order books and ever longer delivery times from suppliers made it necessary to purchase our own cutting machine," recalls Hannes Engl, production and plant manager at Kammerer Tankbau GmbH. After multiple visits to trade fairs, internet research and discussions with various manufacturers, the company went in search of a suitable universal machine for sheet metal, pipe and dome processing. Among the several compared offers, MicroStep’s
MG plasma cutting machine quickly proved the most convincing. "MicroStep offers the entire system and can meet all of our requirements with the machine. The package was just right,” says Mr. Engl.
Accurate weld seam preparation can be done accurately and reliably thanks to MicroStep´s plasma rotator with the patented auto-calibration unit ACTG.
“We work much faster, more efficiently and more flexibly”The investment in the plasma cutting machine has brought Krammerer Tankbau new flexibility and speed: "When manufacturing a
tank bottom, we save a day of time compared to the previous manual cutting," reports Mr. Engl with satisfaction. Since it went into operation in January 2022, the multifunctional 3D cutting machine has been in continuous single-shift operation; two-shift operation is planned in the future. Accurate
weld seam preparation is particularly important for Kammerer Tankbau when cutting sheet metal for storage tanks – thanks to the integrated
plasma rotator and its
auto-calibration unit ACTG, this can now be done accurately and reliably on different types and shapes of material.
The system is supplemented by a 26 kW drilling unit capable of making up to Ø40 mm holes, tapping up to M33 and countersinking with a linear magazine with 8 positions for automatic tool exchange.
The system is supplemented by a
26 kW drilling unit capable of drilling holes up to Ø40 mm, tapping up to M33 and countersinking, with a linear magazine with 8 positions for automatic tool exchange. The work area consists of a cutting table that can fit two 6 x 3 m plates end-to-end with a pipe cutting channel for cutting
pipes and closed profiles up to Ø500 mm and a dome cutting table in the front of the machine for domes up to Ø3600 mm. “We are absolutely satisfied with the technology. Purchasing the system was worth it for us because we can now work much faster, more efficiently and more flexibly”, says Mr. Engl. The cooperation with MicroStep also convinced the production and plant manager that it was the right choice: “Everything works smoothly. Good service is particularly important to us – and it works extremely well.”
“We are absolutely satisfied with the technology. Purchasing the system was worth it for us because we can now work much faster, more efficiently and more flexibly,” says Hannes Engl, production and plant manager at Kammerer Tankbau GmbH.