During 29 years of its existence, MicroStep has grown into a renowned supplier of CNC cutting machines for industrial applications. Thanks to the cooperation with a Finnish integrator Pemamek Oy, whole new horizons of possibilities have opened up.
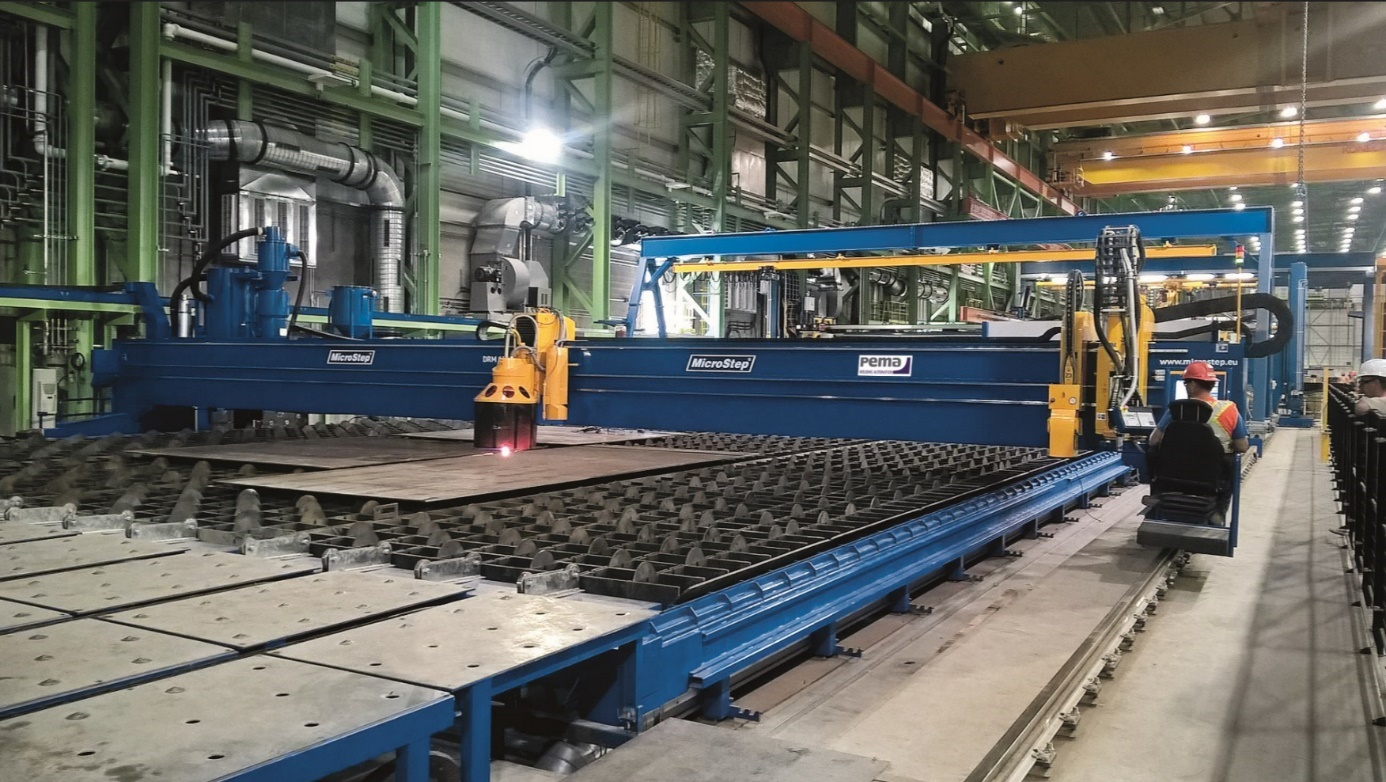
Fig. 1 Large-scale cutting device with a working area of 16x12m in Irving Shipbuilding shipyards (Halifax, Canada)
Today, more than 2800 MicroStep machines work in over 55 countries all around the world. Every year approximately 180 CNC machines worth about 32 million euros are produced and 95% are sold abroad. The CNC machines come in lengths ranging from 3 to 50 meters and widths from 1.5 to 24 meters. In many cases the supplied machines are complex cutting systems custom designed and constructed to satisfy production needs of the customer.
The company offers CNC machines used primarily for plasma, oxyfuel, fiber laser and high pressure waterjet cutting. These machines may be equipped with combination of aforementioned technologies as well as other technologies- the most common being drilling, tapping, countersinking and marking using different methods (plasma, laser, inkjet or vibrating micro percussion pen). These are often complicated systems producing complete parts which do not have to be machined further. When requested, these CNC machines may be augmented with systems for automatic loading and unloading. These fully automated production units provide high productivity while requiring minimal manual labor of the operator.
Success of the company is a result of continuous development focused on improving products as well as on creating new products in order to meet even the most rigorous customer demands.
Applications
The area of application of CNC cutting machines is quite large. They are used for simple metal sheet cutting (up to thickness of 300 mm) but also for cutting of complex 3D parts such as high pressure container caps, different profiles (V, Y, and K cross sections), pipes, etc. It was the research into 3D cutting that allowed MicroStep to access the complicated cutting applications market.
One of the prominent application areas of CNC cutting machines is shipbuilding where the machines are used not only for standard cutting applications but also in automated technology lines for production of large-scale panels (fig.1). These CNC machines are capable of cutting large scale parts with dimension ranging from 16x16m up to 24x24m. Cutting is not the only part of the process, the workpiece for these parts is created by welding multiple metal sheets together in the previous section of the line. That is why these projects are realized under the patronage of finnish welding automation and integration expert company Pemamek Oy Ltd.
The peculiarity in this case is that the thickness of the workpiece varies. Apart from the usual cutting heads (usually plasma or oxyfuel) which allow for bevel cutting (V, Y, K cuts), the machine is also equipped with a blasting and a marking head. Blasting head is used to clean the primer from certain areas on the workpiece where, subsequently, suspension profiles are welded. The blasting head is equipped with a marking plasma torch, which is marking the exact spot for the suspensions. The marking head allows adding signs or description on the workpiece.(fig.2)

Fig. 2 Blasting and marking head equipped with plasma torch Hypertherm HPR130xD
Cutting of large-scale panels
CNC machines for cutting of large scale parts have added features connected with cutting unevenly thick large metal sheets but also certain special features. An example is a system for measuring the position of the workpiece and afterwards setting the starting point of the cutting program. Standard machines set the starting point according to the edges of the plate and its orientation, which are calculated based on points on the edges of the metal sheet detected by a point laser sensor. In case of large scale metal sheets, the starting point has to be set in relation to the position of welds on the panel since the finished product has exactly defined weld positions. Identification of the welds is done by line laser scanner mounted on a rotary support, which allows identifying welds in any direction. Special technology used with these machines is also simultaneous blasting and plasma marking. The marking burner automatically rotates around the blasting head. Their relative position depends on the direction in which the device is moving and thickness of the suspension profile since the marked line serves for the correct suspension positioning.

Fig. 3 Mobile operator stand of the large-scale panel line with touch screen control console
Plates of different thickness which make up the panels and the welds between them require complex control of the plasma cutting process. Metal sheets of different thickness require different cutting parameters like the cutting speed or the cutting current. Change between different sheet thickness is linear with surface inclination ranging from 1:4 to 1:3 so the parameter change is not sudden but linearly interpolated. The most complicated issue with these machines is the cutting height control. The classic height control for constant plasma arc voltage is not enough in this case. If the thickness change happens on the top side of the panel the cutting height has to be controlled in the robotic mode according to the defined shape of the weld. After the change to new thickness happens new parameters are measured and the height regulation is turned on again. When crossing welds, the height control needs to be deactivated so that the cut contour is not deformed.
The ability to supply large scale CNC machines for ship construction and the related cooperation with the company Pemamek Oy Ltd. has catapulted MicroStep among world’s foremost producers of CNC cutting machines. First such machine has been supplied to Irving Shipbuilding shipyards in Halifax. Currently, another panel cutting line is being installed at Vard Tulcea shipyards in Romania and future installations include applications for MV Werften (GER). STX shipyards in France ordered large scale fiber laser cutting machine with working area 50x3 m large.
Large-scale CNC cutting machines represent only a fraction of company’s portfolio. Ever since its humble beginnings, MicroStep has been trying to always meet the customer’s needs in the largest extent possible.
If you wish to know more about Panel Lines and our partner Pemamek, here is their website.